Роль заполнителей в бетоне
Заполнители, занимающие основную часть объема в смеси, выполняют ряд важных функций, в том числе:
- формирование жесткой основы бетонного раствора;
- уменьшение усадки при твердении до 10 раз;
- повышение прочности бетона;
- снижение теплопроводности, улучшение теплоизоляционных характеристик — при использовании пористых заполнителей;
- уменьшение ползучести раствора;
- регулирование плотности бетона за счет добавления тяжелых или легких заполнителей.
Из этих функций понятно, что заполнители непосредственно влияют на качество готового бетона. Выбор их вида позволяет добиваться требуемых свойств смеси и регулировать их.
Виды заполнителей для бетона
В зависимости от размера фракции заполнители бетона бывают мелкие и крупные. Обе разновидности используются при приготовлении бетонного раствора. Рассмотрим особенности мелких и крупных заполняющих материалов в классификации.
Мелкие
В качестве мелкого заполнителя для бетона используется песок — природный или искусственный.
Природный песок — сыпучий неоднородный мелкозернистый материал, который образуется в результате естественного разрушения или дробления горных пород. Его добывают на месторождениях. Крупность зерен песка составляет до 5 мм.
Классификация песков природного происхождения предполагает их деление по следующим признакам:
- По условиям образования. Морские, речные, овражные пески. Морские и речные отличаются гладкой поверхностью и округлой формой зерен. Овражный песок характеризуется угловатой формой и неоднородной фракцией зерен, в его составе может содержаться большое количество органических, глинистых включений.
- По составу. Выделяют пески кварцевые (силикатные), карбонатные, полевошпатные.
Искусственный песок — сыпучий мелкозернистый материал, который получают в результате искусственного дробления горных пород с соблюдением технологии, предусмотренной ГОСТ. Также его производство может осуществляться путем дробления разных видов промышленных продуктов. Искусственный песок отличается шероховатой поверхностью и остроугольной формой зерен, их однородным размером. При соблюдении технологии производства в соответствии с нормами ГОСТ в составе искусственного песка отсутствуют примеси, ухудшающие качество бетона.
Важным критерием классификации является крупность мелкозернистого заполнителя бетона. Это неоднородный показатель. Мелкий заполнитель для бетона имеет размер зерен от 0,6 до 5 мм. Использование песка в качестве мелкого заполнителя для производства бетона зависит от преобладающего размера зерен в составе. Для его определения используется модуль крупности. Это показатель, который определяется эмпирическим путем по методике предусмотренной ГОСТ 8736-2014.
Классификация мелкого заполнителя по модулю крупности приведена в таблице:
Вид песка |
Модуль крупности |
повышенной крупности |
3,0-3,5 |
крупный |
2,5-3,0 |
средний |
2,0-2,5 |
мелкий |
1,5-2,0 |
очень мелкий |
1,0-1,5 |
тонкий |
0,7-1,0 |
очень тонкий |
до 0,7 |
При использовании песка в качестве мелкозернистого заполнителя для бетонов и растворов он вводится в состав в минимальном количестве, обеспечивающем требуемую вязкость смеси. От крупности его зерен зависит требуемое количество цемента для раствора. При использовании мелких песков повышается расход цемента. Чтобы повысить экономическую эффективность производства бетона, мелкий песок часто обогащают. Для этого в его состав добавляют песок с более высокой крупностью зерен.
Фракция мелкого заполнителя бетона в значительной мере влияет на характеристики смеси. Для легких кладочных и монтажных растворов используют песок с модулем крупности 1,5-2,5. На производство тяжелого бетона идет песок с модулем крупности 2-3,25.
Важным критерием качества мелкозернистого заполнителя является чистота состава. Присутствующие в составе глинистые и пылевидные примеси приводят к значительному увеличению вязкости бетона. Это ограничивает объем песка, который можно ввести в состав смеси. Поэтому содержание таких примесей должно контролироваться. Это требование не такое жесткое для составов невысоких марок, например, для бетона М100. Для растворов от марки от М200 такие ограничения должны строго соблюдаться. Например, в мелком заполнителе бетона В25 содержание таких примесей не должно превышать 3 % по весу. При этом содержание глины не должно составлять больше 0,5 % по весу.
Также мелкий заполнитель не должен содержать органических кислот. Их присутствие в составе приводит к расходу выделяемой при гидролизе цемента свободной извести, которая идет на нейтрализацию органических кислот. Это приводит к снижению качества бетона.
Крупные
Крупный заполнитель для бетона в значительной мере определяет его прочность, плотность, устойчивость к усадке. Его доля в стоимости готового раствора может достигать 15 %.
Классификация заполнителей бетона крупной фракции по плотности зерен включает такие основные виды:
- Плотные. Имеют плотность выше 2,0 г/см3. Используются для производства тяжелых бетонов.
- Пористые. Имеют плотность менее 2,0 г/см3. Применяются для изготовления легких смесей.
Плотные крупные заполнители
Это самый распространенный вид заполнителей для бетона. Он включает такие основные природные материалы:
- гравий;
- щебень из гравия;
- щебень.
Гравий — зернистый неорганический материал с фракциями 5-20 мм. Он добывается на природных месторождениях методом рассева песчано-гравийных или гравийно-песчаных смесей. Его прочность составляет около 800 кг/см2. Гравий имеет зерна с закругленными краями, что ухудшает его сцепные свойства. В сочетании со сравнительно небольшой прочностью это обуславливает его применение для приготовления тяжелых бетонов класса до В25, реже — до В30. Морозостойкость составов на гравии обычно находится в пределах F100-F150, что ограничивает его применение в условиях частых циклов замерзания-оттаивания. При этом плюс гравия состоит в его меньшей стоимости по сравнению со щебнем, что уменьшает расходы на производство бетонного раствора.
Щебень из гравия производят методом дробления гравия высоких фракций, валунов, гальки. Количество дробленых зерен в его составе должно быть не менее 80 %. Их крупность, как и гравия, составляет 5-20 мм, прочность — около 800 кг/см2. При этом благодаря преобладанию в составе дробленых зерен улучшаются сцепные свойства. По своим характеристикам этого заполнитель занимает промежуточное место между гравием и щебнем.
Щебень — неорганический материал, который получают методом дробления плотных, массивных горных пород, например, гранита. При дроблении образуются куски камня размером 5-70 мм. Они отличаются шероховатой поверхностью и угловатой формой. Благодаря этому улучшается сцепление с другими компонентами смеси. Прочность щебня составляет в среднем 1200 кг/см2. Также он имеет высокую морозостойкость — в среднем F300-F400. Щебень используется в качестве крупного заполнителя для производства тяжелых бетонов, применяемых в строительстве зданий, сооружений, железобетонных конструкций, рассчитанных на значительные эксплуатационные нагрузки.
Основные требования к заполнителям для тяжелого бетона касаются их прочностных параметров. Так, крупный заполнитель должен иметь прочность, превышающую в 1,5-2 раза прочность изготавливаемого бетона. Определение прочностных параметров производится методом испытания на сжатие в увлажненном состоянии образцов породы в виде выпиленного куба или цилиндра высотой 40-50 мм. Доля зерен выветренных или малопрочных пород в составе крупного заполнителя (гравия или щебня) для тяжелых бетонных смесей не должна превышать 10 % по массе.
Кроме этого, действуют требования по морозостойкости щебня или гравия. Она должна быть не ниже целевой морозостойкости тяжелого бетона. Испытания на морозостойкость производятся методом поочередного замораживания и оттаивания образцов породы в увлажненном состоянии. По результатам испытаний присваивается марка от F150 до F400, которая указывает на количество циклов, которые материал выдерживает без разрушения и потери прочностных параметров.
Пористые крупные заполнители
Крупные пористые заполнители применяют для производства легких бетонов. Эти материалы уменьшают плотность и вес бетонной смеси. Соответственно, снижается и прочность. При этом их пористая структура улучшает теплоизоляционные и звукоизоляционные качества. Бетоны, произведенные с использованием этого вида заполняющих материалов, применяют для возведения конструкций, для которых снижение веса и повышение изоляционных свойств преобладает над прочностными параметрами. Основная сфера применения — жилищное и малоэтажное строительство.
Классификация крупных пористых заполнителей для бетона по происхождению включает природные и искусственные материалы.
Природные заполнители бетона
Природные пористые заполнители получают методом дробления горных пород. Основные виды таких пород:
- пемза;
- вулканические шлаки;
- вулканические туфы;
- известковые туфы.
Пемза — горная порода вулканического происхождения, которая образуется в результате быстрого застывания насыщенных газами кислых и средних лав. В ее состав входит до 75 % кварца и до 25 % полевых шпатов (обычно ортоклаза). Это вспененный камень пористой структуры, в которой объем пор достигает 80 % общего объема. Такая структура делает пемзу эффективным теплоизоляционным материалом. Плотность пемзы составляет в среднем 300-900 кг/м3. В отличие от вулканического туфа материал имеет однородный состав.
Вулканические шлаки — продукты извержения вулканов. Они образуются при выбросе из кратера вулкана обрывков пузыристых лав во время взрывов, которые застывают во время полета. Источником их образования служат жидкие магмы, из которых достаточно легко удаляются газы. Вулканические шлаки могут иметь разнородный состав. Их структура отличается большим количеством крупных пор. Часто поры имеют сильно вытянутую, неправильную форму и разделяются достаточно толстыми перегородками.
Вулканические туфы — осадочные горные породы сложного состава. Его основу составляет вулканический пепел в смеси с вулканическими бомбами и другими обломками. Также имеются примеси невулканического происхождения. В процессе формирования породы ее компоненты хорошо уплотняются и скрепляются между собой. Вулканические туфы имеют обломочно-пористую структуру и неоднородный состав. Основная масса материала содержит поры. При этом в нее могут включать обломки разной формы и размеров. Показатель пористости может достигать 40 %, плотность — 1400-2500 кг/м3.
Известковые туфы, или пористые известняки, — относятся к осадочным горным породам. Они образуются в результате быстрого химического осаждения карбида кальция из подземных источников при их выходе на поверхность. Этот вид туфа имеет игольчато-волокнистую или микрозернистую структуру с занозистым изломом. Показатель пористости материала составляет до 40 %, плотность — в пределах 1550-2600 кг/м3.
Искусственные заполнители бетона
Искусственные легкие заполнители для бетона крупной фракции делятся на специально выпускаемые материалы и получаемые в качестве отходов промышленного производства.
К основным видам специально выпускаемых материалов относятся:
- керамические заполнители для бетона;
- шлаковая пемза;
- перлит.
Основные виды заполнителей, получаемых в качестве отходов производства, — пористые металлургические шлаки и топливные шлаки.
Основные виды керамических пористых заполнителей для изготовления легкого бетона — керамзит и аглопорит.
Керамзит используется в виде керамзитового гравия. Это материал, который получают методом обжига при температуре до 1200 °C гранулированной вспучивающейся глины. Технология предусматривает получение гранул округлой формы, которые в изломе имеют структуры заставшей пены. Благодаря спекшейся оболочке гранулы имеют однородную прочную поверхность. Их размер составляет 5-40 мм. Материал отличается малым весом. Его насыпная плотность составляет 250-800 кг/м3. Прочность керамзита достигает 6 МПа. Используется для производства бетонных растворов с повышенными теплоизоляционными качествами.
Аглопорит — искусственный материал, получаемый при помощи технологии спекания шихты, состоящей из легкоплавких глин и лессовых пород, углесодержащих шахтных пород, топливных шлаков, золы с добавлением топлива в доле 8-10 % по массе. Выпускается в виде гравия или щебня. Средняя плотность материала составляет 500-900 кг/м3. Аглопорит применяют в качестве заполнителя для изготовления жаростойких бетонов.
Шлаковая пемза — искусственный заполнитель для легких бетонов, который изготавливают из металлургического шлака. Технология производства шлаковой пемзы предусматривает быстрое охлаждение расплава шлака вод воздействием водяного пара или воды. Этот процесс сопровождается вспучиванием материала с формированием пористой структуры. Крупные куски материала дробят с получением поризованного щебня.
Вспученный перлит — искусственный материал, который изготавливают из природного перлита, стеклообразной горной породы вулканического происхождения, содержащей до 10 % химически связанной воды. Технология предполагает быстрый нагрев породы до температуры 1100-1200 °C. При этом происходит выделение воды, перлит вспучивается, увеличиваясь в объеме до 10-20 раз. Крупные куски материала дробят с получением щебня, который используется как заполнитель для легкого бетона.
Металлургические и топливные шлаки получают в качестве отходов или побочных продуктов в металлургии и энергетической отрасли. Гранулированный металлургический шлак имеет пористые зерна размером до 10 мм. При добавлении в смесь он позволяет получать бетоны сравнительно малого веса с достаточно высокой прочностью. Топливный шлак образуется в топке в процессе спекания присутствующих в составе угля глинистых примесей. При спекании происходит вспучивание материала, который приобретает пористую структуру. Крупные куски шлака дробят, подвергают рассеву, очищают от остатков золы, несгоревшего угля. В результате получают шлаковый гравий.
Свойства пористых заполнителей
Физико-механические параметры пористых заполнителей в значительной мере определяют характеристики изготавливаемого легкого бетона. Основными свойствами этих материалов, которые имеют значение для технологии, являются:
- прочность;
- плотность;
- пористость.
Эти характеристики определяют соответствующие параметры легкого бетона. Структура пористых заполнителей обуславливает их сравнительно малую прочность и плотность, которые обычно ниже соответствующих показателей готового бетона. Поэтому чем больше заполняющего материала в составе готового раствора, тем он будет менее плотным и прочным.
Для повышения прочностных параметров бетонных смесей на пористых наполнителях в их составе увеличивают содержание цемента. Однако такое повышение прочности доступно только до определенного предела, после которого добавление цемента теряет смысл.
Пористые заполнители имеют характерное свойство поглощать воду при затворении раствора и постепенно отдавать ее в твердеющую смесь. Это улучшает режим твердения, позволяет бетону лучше набрать прочность и плотность.
Основные требования к заполнителям для бетона
Заполнители занимают основную объемную часть бетонной смеси. Учитывая их влияние на характеристики готового бетона, они должны отвечать ряду требований, в том числе:
- В крупных и мелких наполнителях должно соблюдаться определенное соотношение зерен разного размера. Это обеспечивает наиболее полное насыщение объема раствора зернами наполнителя. Для соблюдения этого требования при приготовлении смеси наполнитель отбирается с использованием сит с разной ячейкой, что позволяет получать разные фракции.
- Любой используемый наполнитель не должен отрицательно влиять на процесс твердения, снижать долговечность и эксплуатационные свойства застывшего бетона. Поэтому при его подборе обязательно учитываются параметры прочности материала, морозостойкости, устойчивости к разным видам химических и физических воздействий. Также учитывается структура зерен, минеральный состав заполняющего материала.
- Заполнитель должен быть достаточно чистым. Содержание пылевидных, глинистых, илистых включений приводит к ухудшению сцепления зерен с цементом, поскольку они обволакиваются частицами этих примесей. Поэтому должны соблюдаться предусмотренные по ГОСТ ограничения по максимальному содержанию посторонних включений в наполнителях крупной и мелкой фракции.
Контроль соблюдения требований к заполнителям проводится методом лабораторных испытаний. Специалисты отбирают определенное число образцов материала. После этого каждый образец проходит испытания, результаты которых усредняются и принимаются для всей партии наполнителя.
Влияние заполнителей на качество бетона
Характеристики применяемых заполнителей непосредственно по многим параметрам определяют качество готового бетона.
Наполнители формируют жесткий каркас. Они должны надежно сцепляться с цементным камнем, что обеспечивает высокую стойкость бетонной конструкции к эксплуатационным нагрузкам. При недостаточном сцеплении искусственный камень становится хрупким, легко разрушается под действием поперечных нагрузок. Надежность сцепления зависит от таких основных параметров наполнителя:
- форма зерен;
- чистота поверхности зерен;
- пористость;
- наличие посторонних включений.
Качественный заполнитель повышает прочность бетона после застывания. Кроме этого, он позволяет уменьшить усадку раствора при застывании до 10 раз. После усадки материал набирает полную прочность и морозостойкость.
Для производства товарного бетона или изготовления раствора на стройплощадке должны использоваться чистые мелкие и крупные наполнители. Большое количество загрязняющих включений ухудшается сцепление зерен с цементным камнем. Это может вызывать быстрое разрушение конструкции.
Учитывая, что наполнители занимают основной объем бетона, от них непосредственно зависит его плотность и вес. При использовании пористых материалов вы получаете легкие бетоны с уменьшенной теплопроводностью, улучшенными звукоизоляционными свойствами. Применение плотных заполнителей позволяет получать тяжелые бетонные смеси, которые используются для основных строительных работ и бетонирования.
Применение заполнителей для бетона
Для приготовления качественного бетона нужно подобрать тип мелкого и крупного заполнителя, который будет использоваться в составе смеси. Далее рассчитывается требуемое количество наполнителей в соответствии с нормами ГОСТ. При этом должны учитываться технологические требования к составу, наличие и тип армирования, условия эксплуатации железобетонной конструкции. В том числе учитывается требуемая морозостойкость, жаростойкость, устойчивость к воздействию агрессивных сред, воды, другие критерии. Обязательно учитывают расчетный вес и прочностные параметры монтируемой конструкции.
После подбора заполнителей и расчета их количества эти материалы смешиваются с бетоном для получения сухой смеси. При потребности в ее состав могут вводиться модифицирующие добавки для улучшения эксплуатационных качеств бетона. Далее сухая смесь затворяется необходимым объемом чистой воды. Все компоненты тщательно перемешиваются для получения однородного состава. Готовый бетон используют в соответствии с назначением для бетонирования конструкций, заливки фундаментов, стяжек, монолитного строительства, производства железобетонных изделий или других целей.
Производство бетона
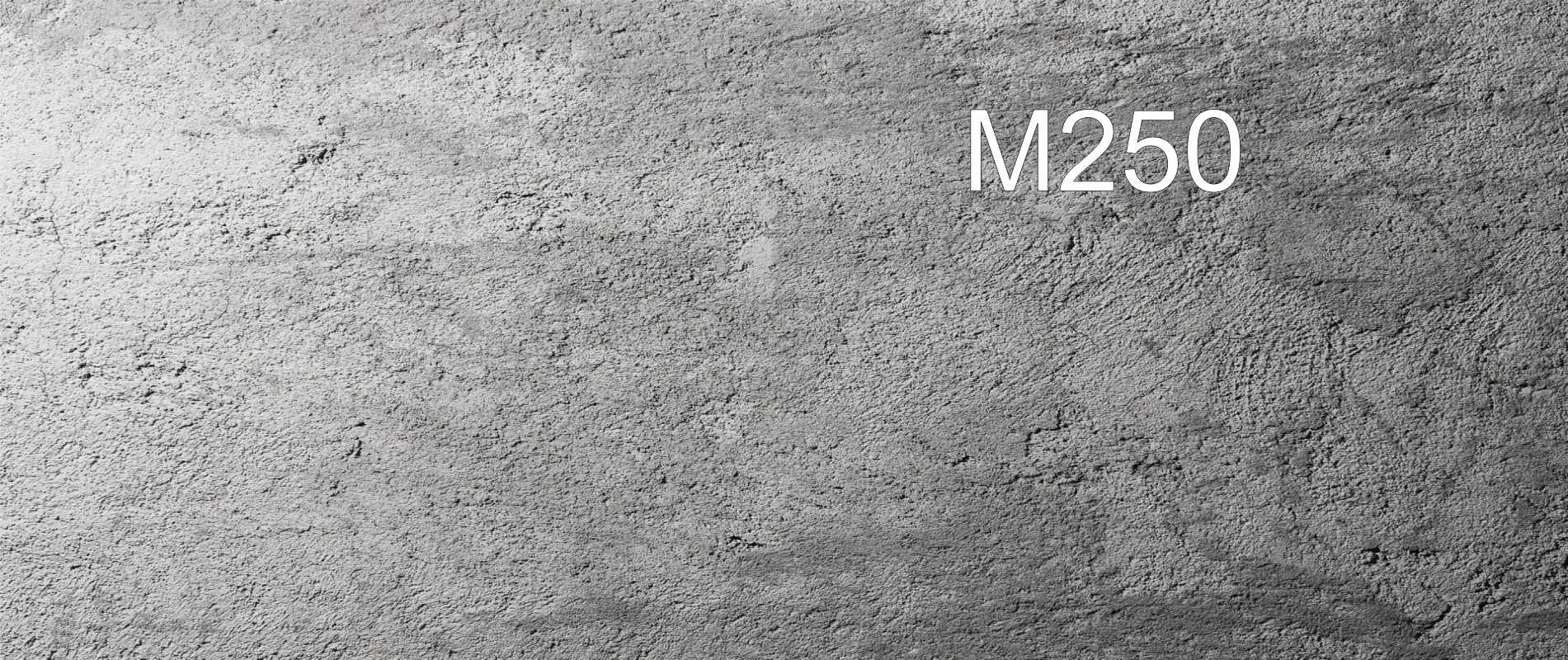
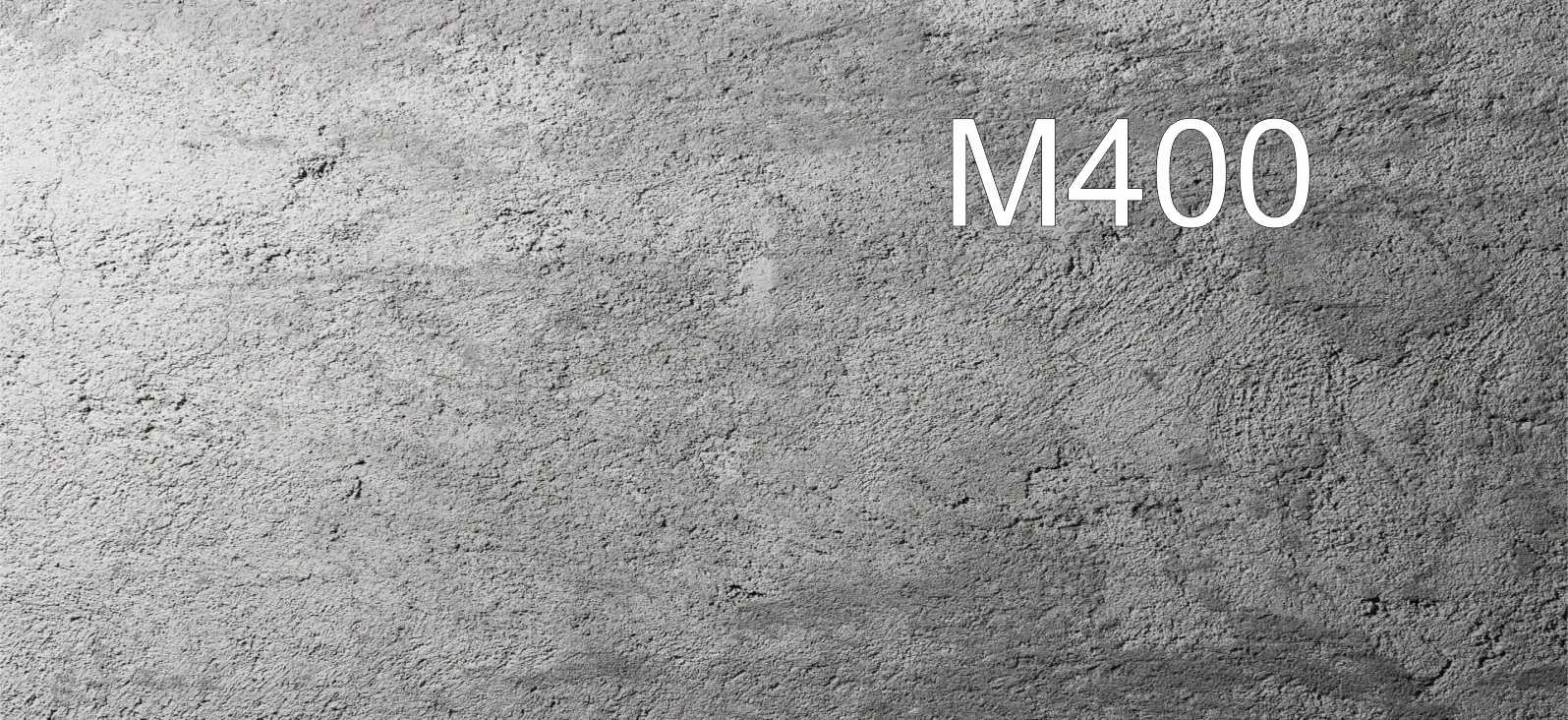
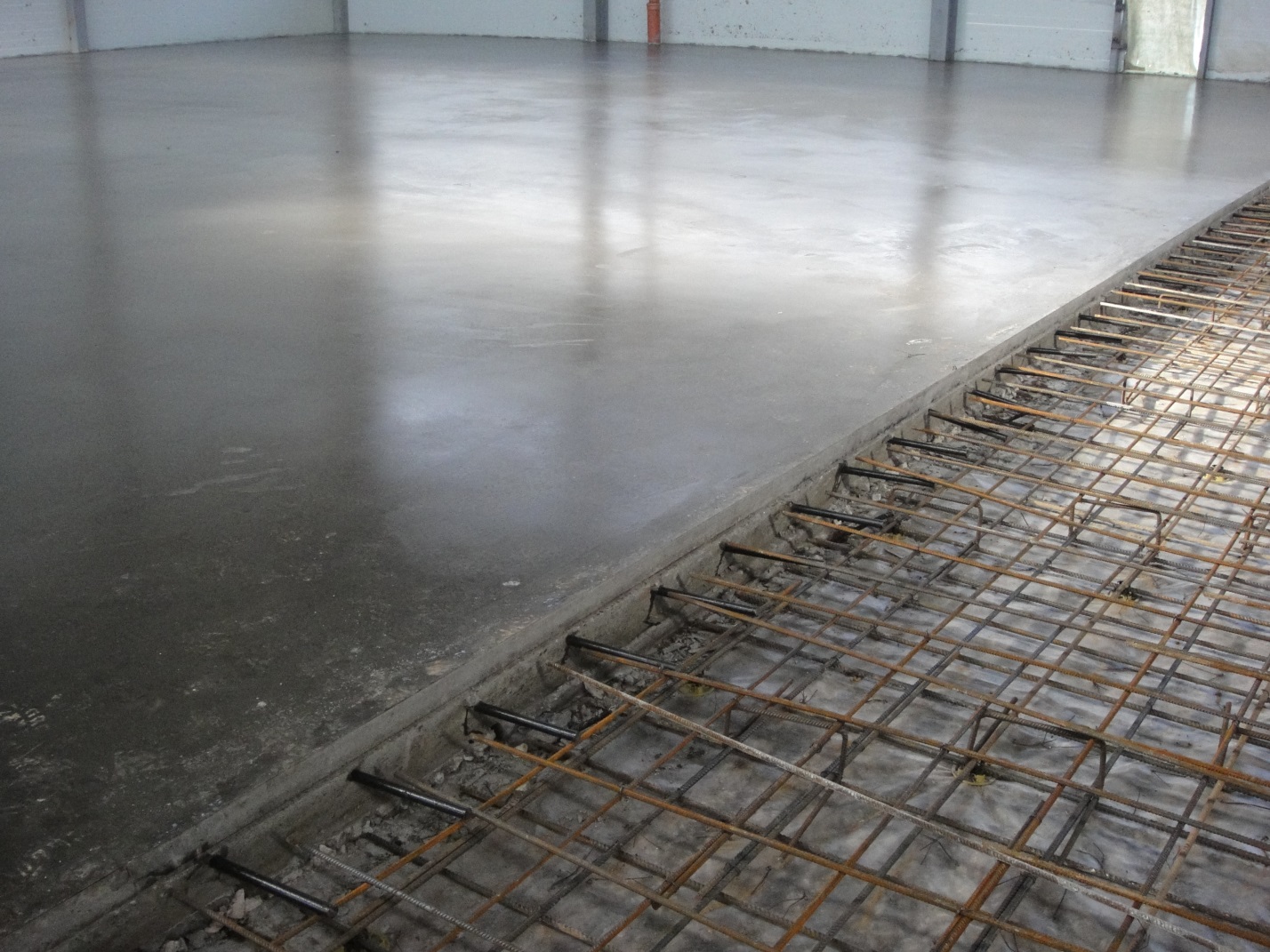
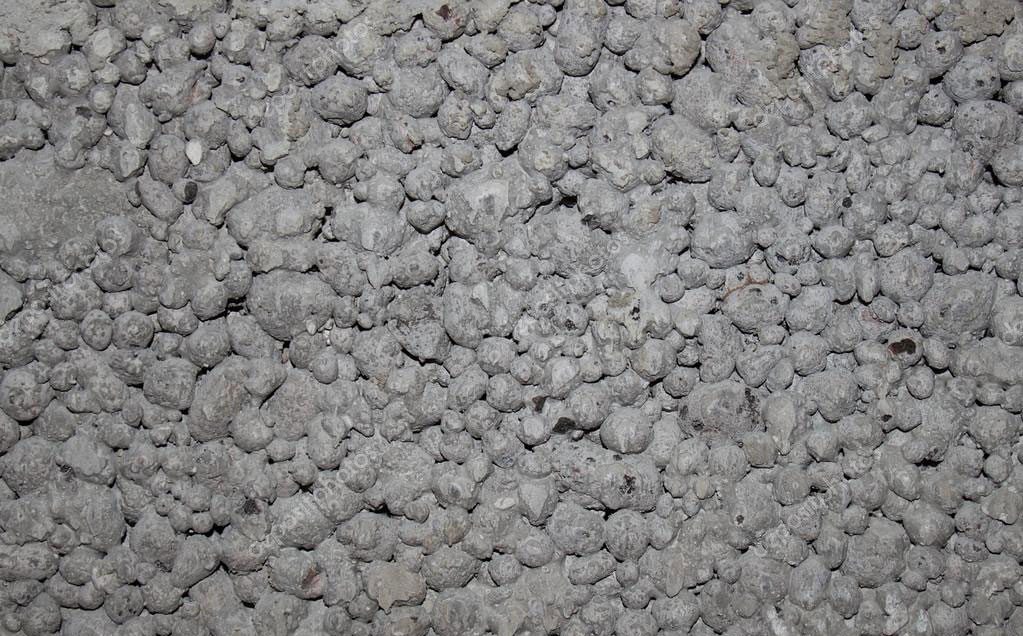
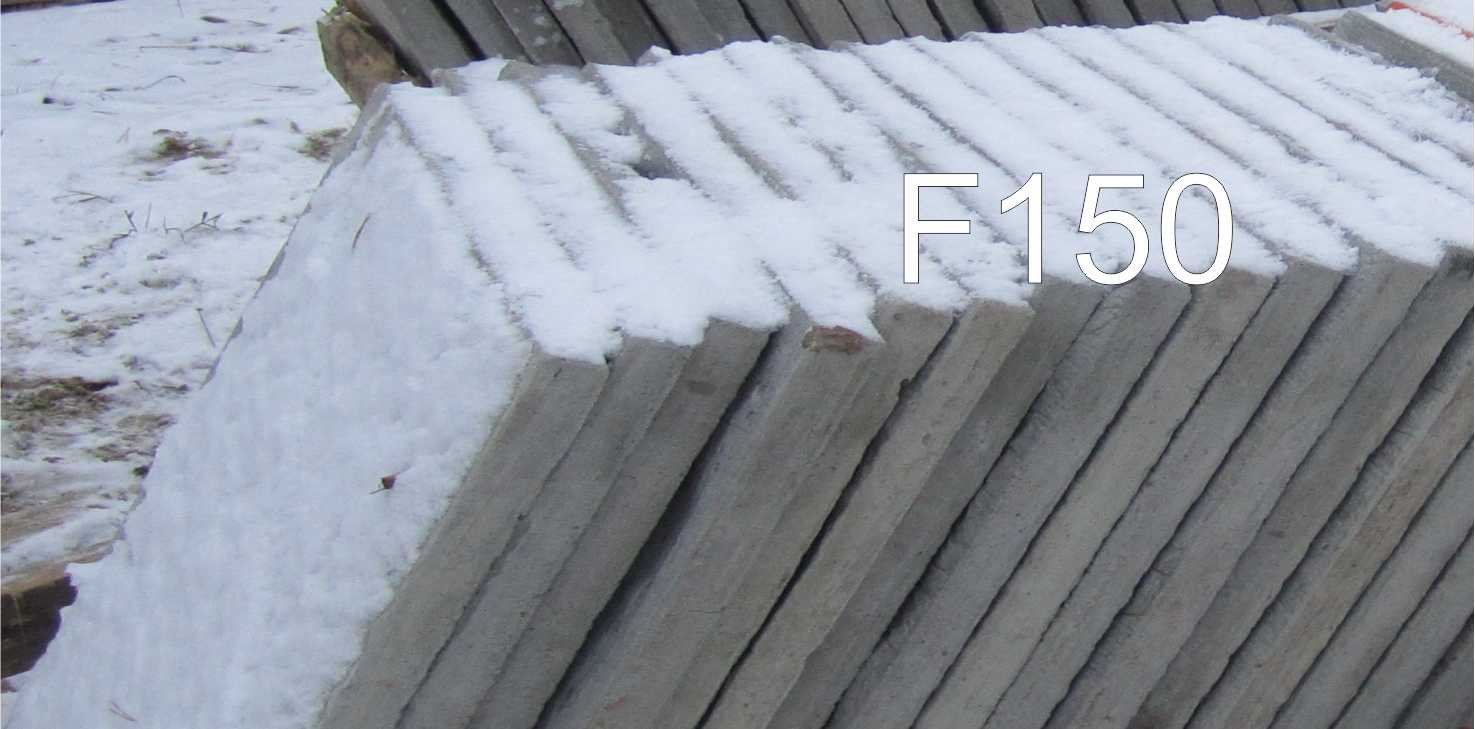
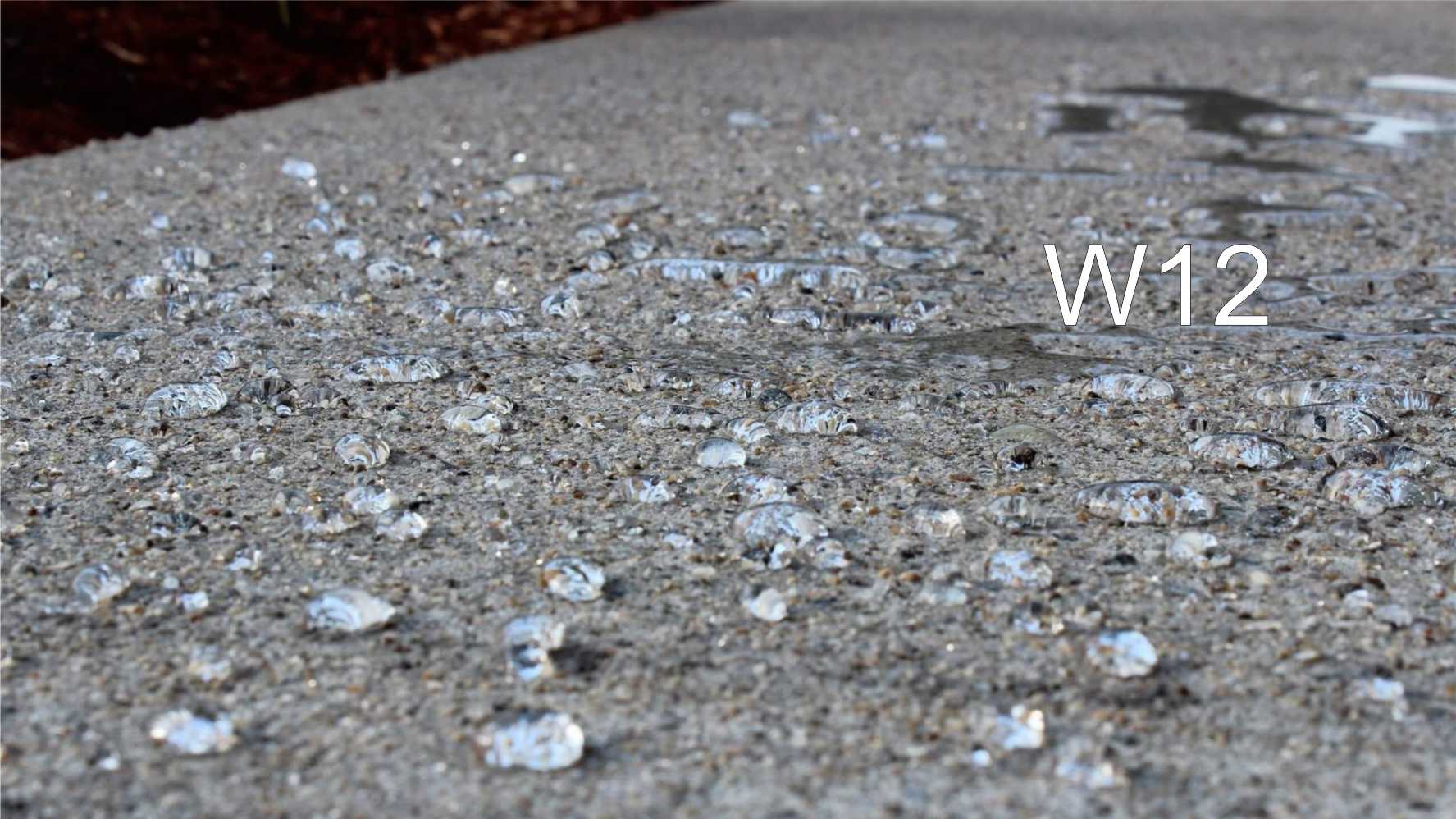